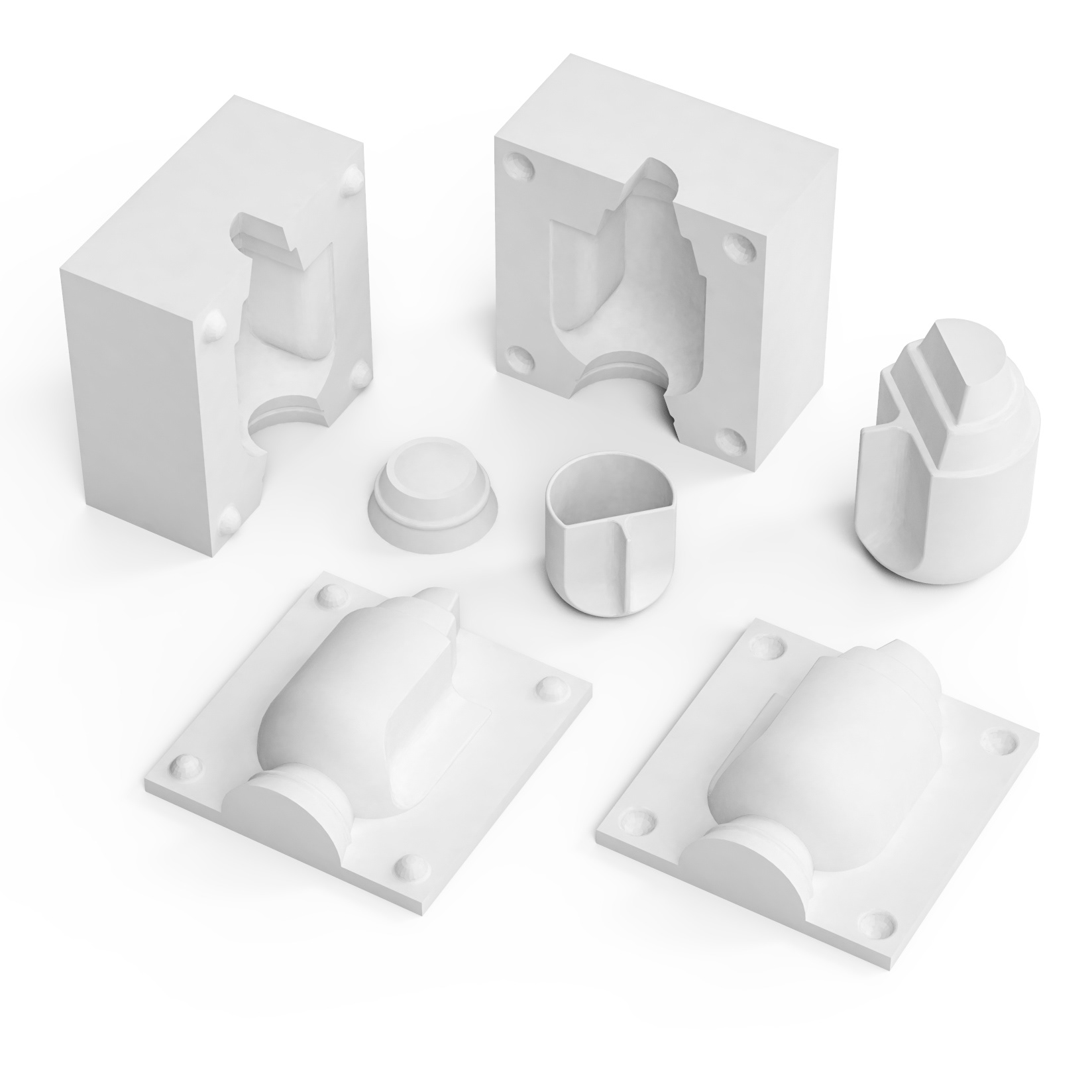
Introduction
Slipcasting is one of the most widespread modes of mass ceramics manufacturing. It is used to produce products like cups and pots. It is a mold-based technique that is used to get many copies of one design. The tradition method of mold making for slipcasting requires technical sculpting skills that make the barrier to entry too high for many people interested in the technique.
I want to increase the accessibility of slipcasting by utilizing rapid prototyping techniques that I have learned to master through my work at the DAAP Rapid prototyping Center. Utilizing rapid prototyping machines to produce molds for slipcasting removes the barrier of mastering sculpting prior to being able to make a mold. Widespread CAD (computer aided design) tools can be used to design the product digitally and then molds can be created through 3D printing or CNC machining. This could greatly increase the accessibility of slipcasting and in turn the ability of people to realize their creative vision.
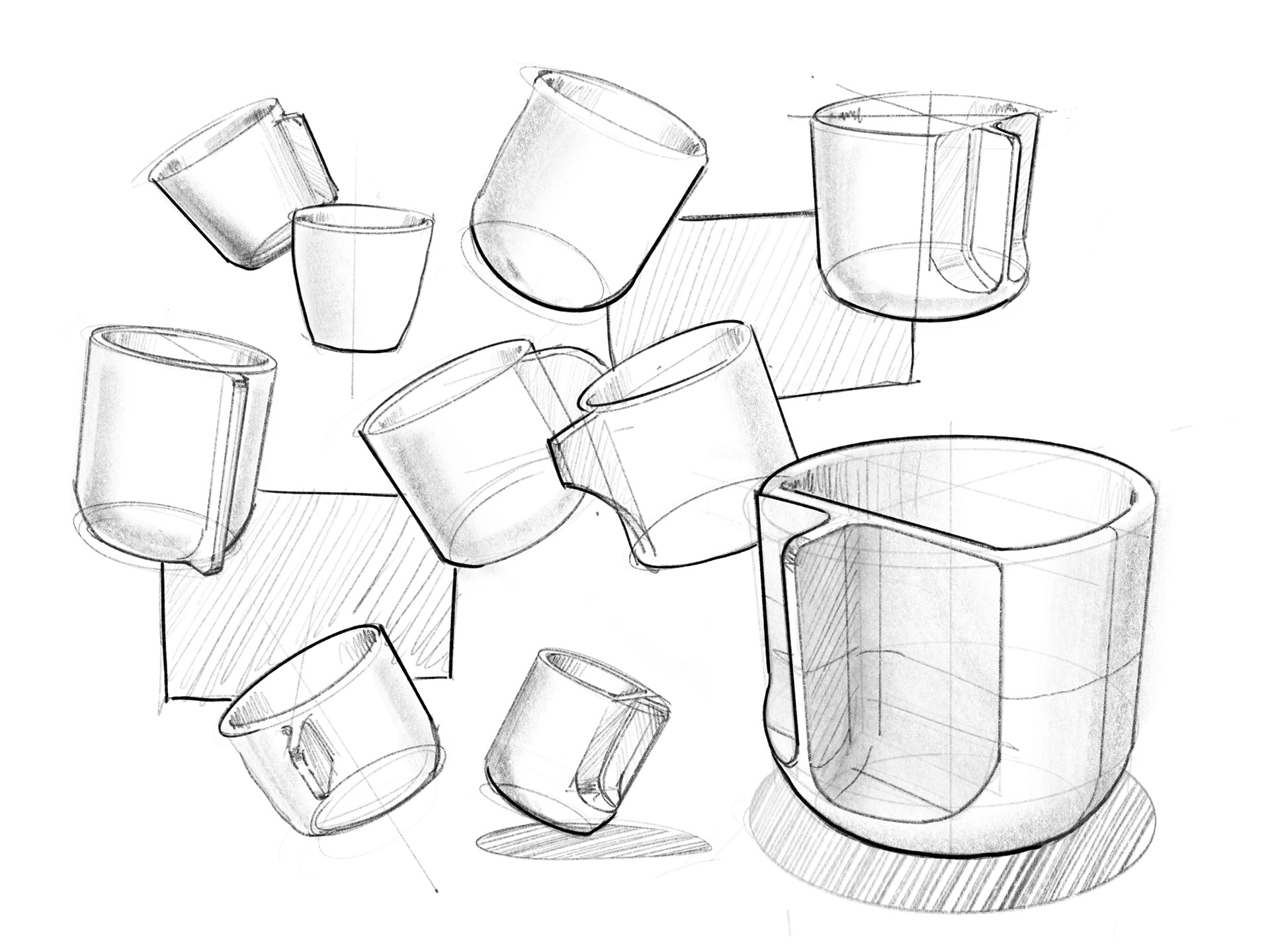
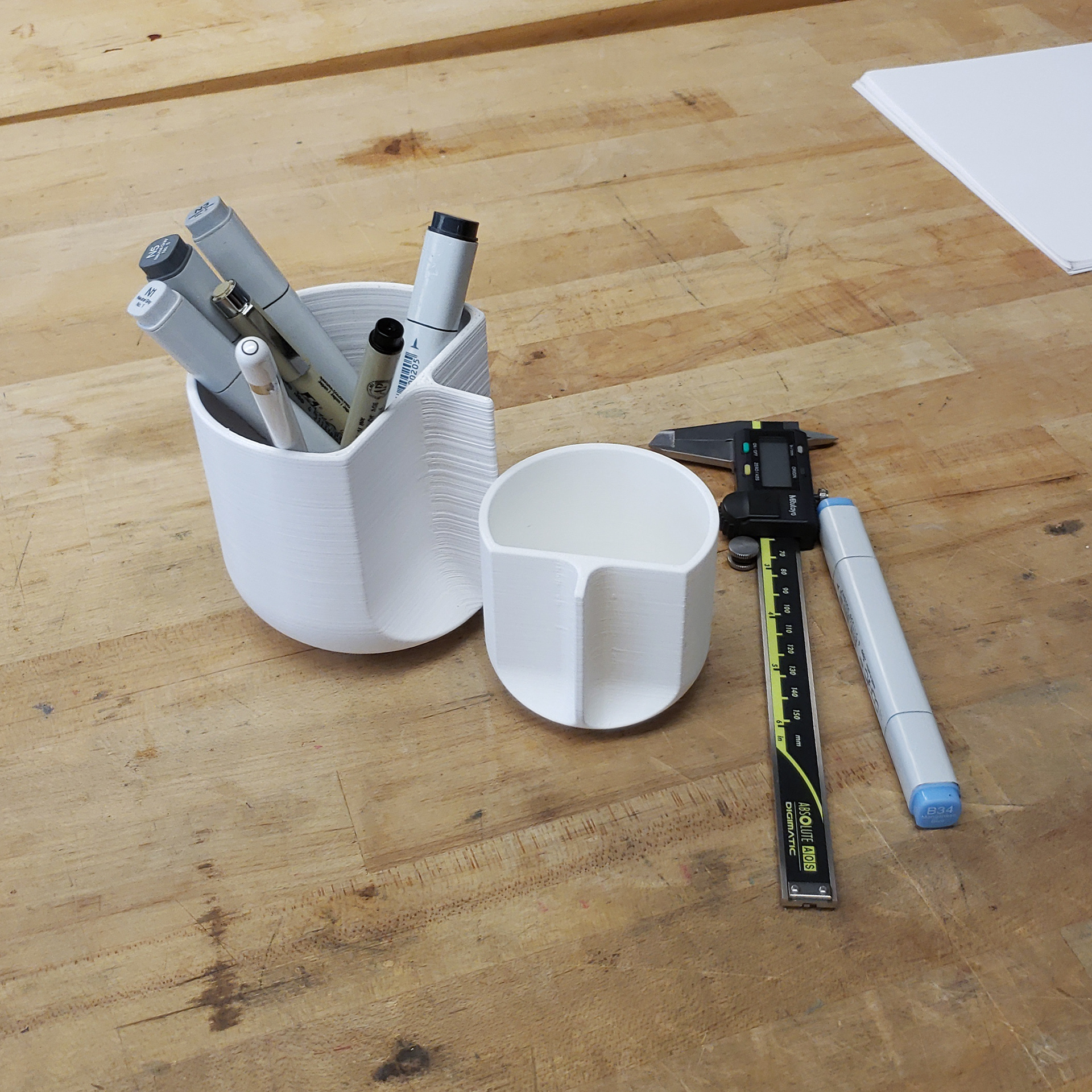
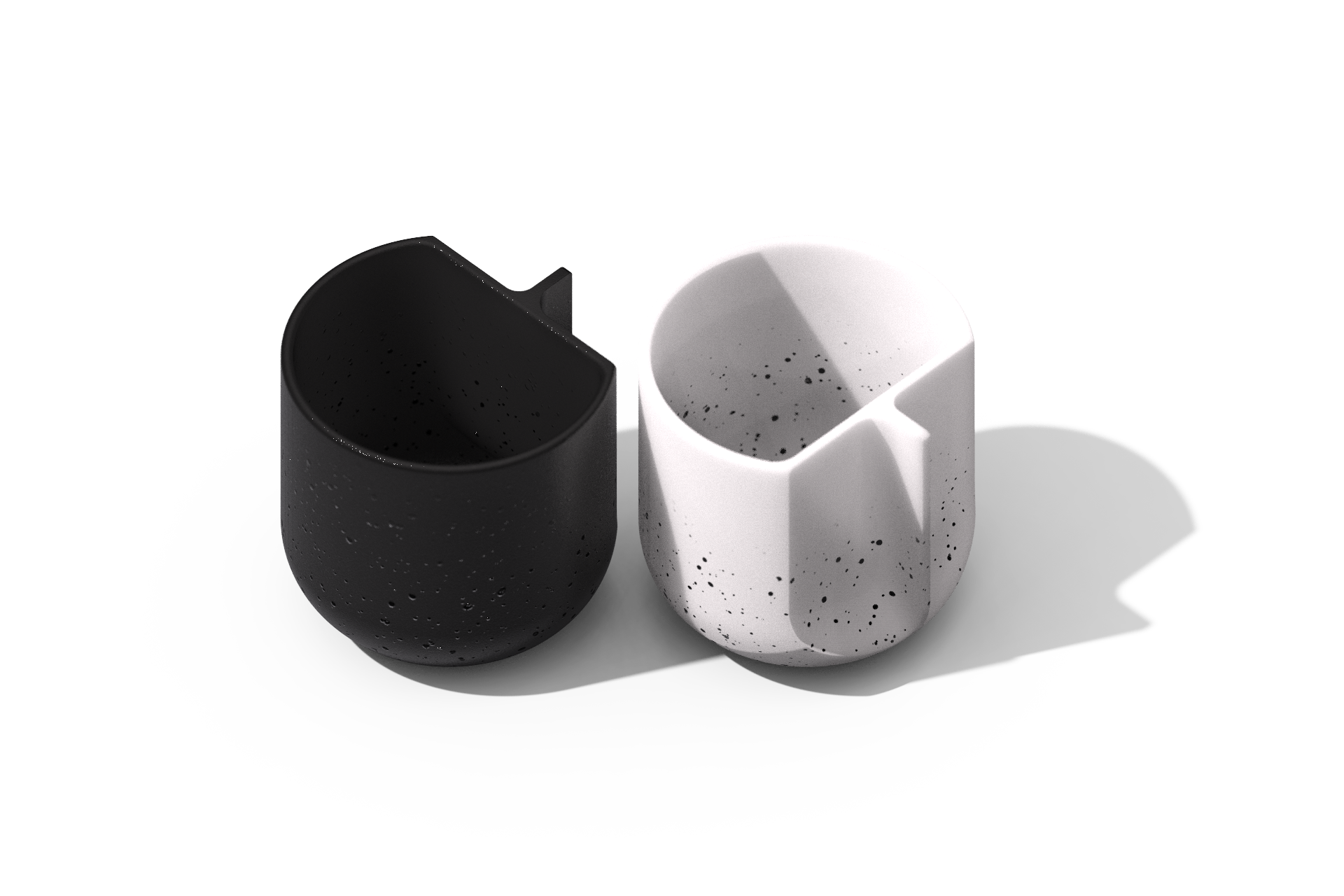
Model Design
I started my process by designing a cup form for slip casting that exhibited some of the unique capabilities of the process. I began sketching around a coffee cup concept and landed on a minimalist interpretation of a coffee cup where the handle is carved into the cup form allowing for a simple place to grip the cup (top left image). I quickly modeled the cup up and began experimenting with sizes and proportions through 3D printing prototypes (top right image). Once I was comfortable with the design I created experimented with different finishes through computer rendered visualizations (left). This allowed me to get an idea of what the finished product would look like without investing time and money in making anything for real.
The process of designing the cup virtually, quickly validating and iterating with 3D prints demonstrates the increased accessibility of this process as the conventional approach would be hand throwing or sculpting prototypes. In contrast to this manual, time-intensive workflow, the virtual process allows the application of more widespread design tools that many more School of Design students have already developed.
Mold Design
The next step was design the slipcasting molds themselves. Slipcasting works by filling a plaster mold with a watery clay solution called slip. The plaster in the mold absorbs water out of the solution, drying a thin wall where the slip interfaces with the mold. After sometime the excess slip is poured out and the mold is opened leaving thin walled pottery ready to be fired.
Traditionally the plaster mold is made from a positive of the final model that must be sculpted at a 10% scaled volume to account for the shrinkage of the final part during firing. The plaster mold is created off of this positive by casting half of the object at a time in plaster to get a two part negative mold that is ready for the slip casting process (to the right you can see an image of a two part mold from this project)
The goal for me was to designs methods of using rapid prototyping tools to create molds quickly from digital designs. There were two methods of rapid prototyping that I pursued with my research. 3D printing, and CNC machining as they are the two most prevalent rapid prototyping technologies.
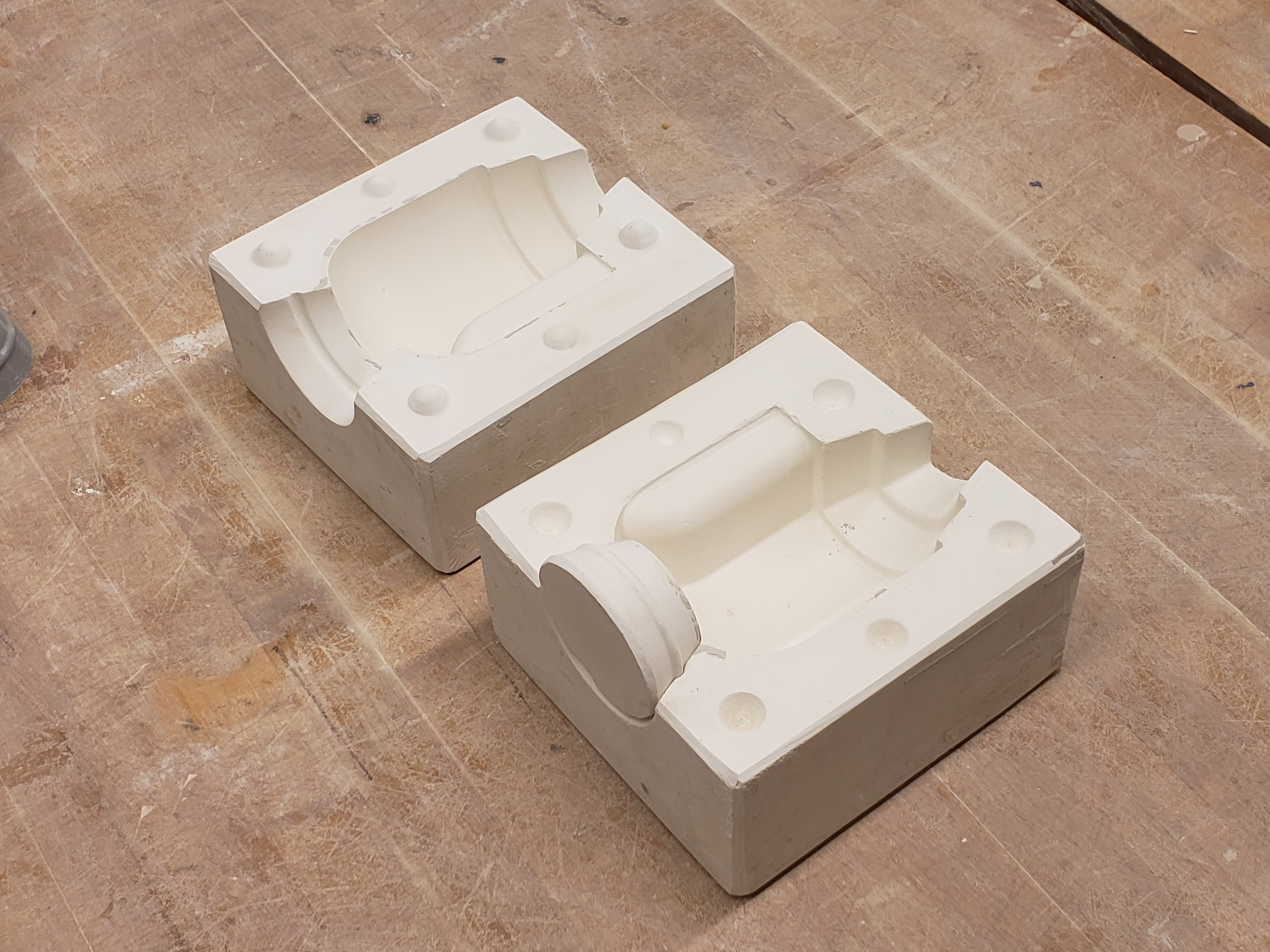
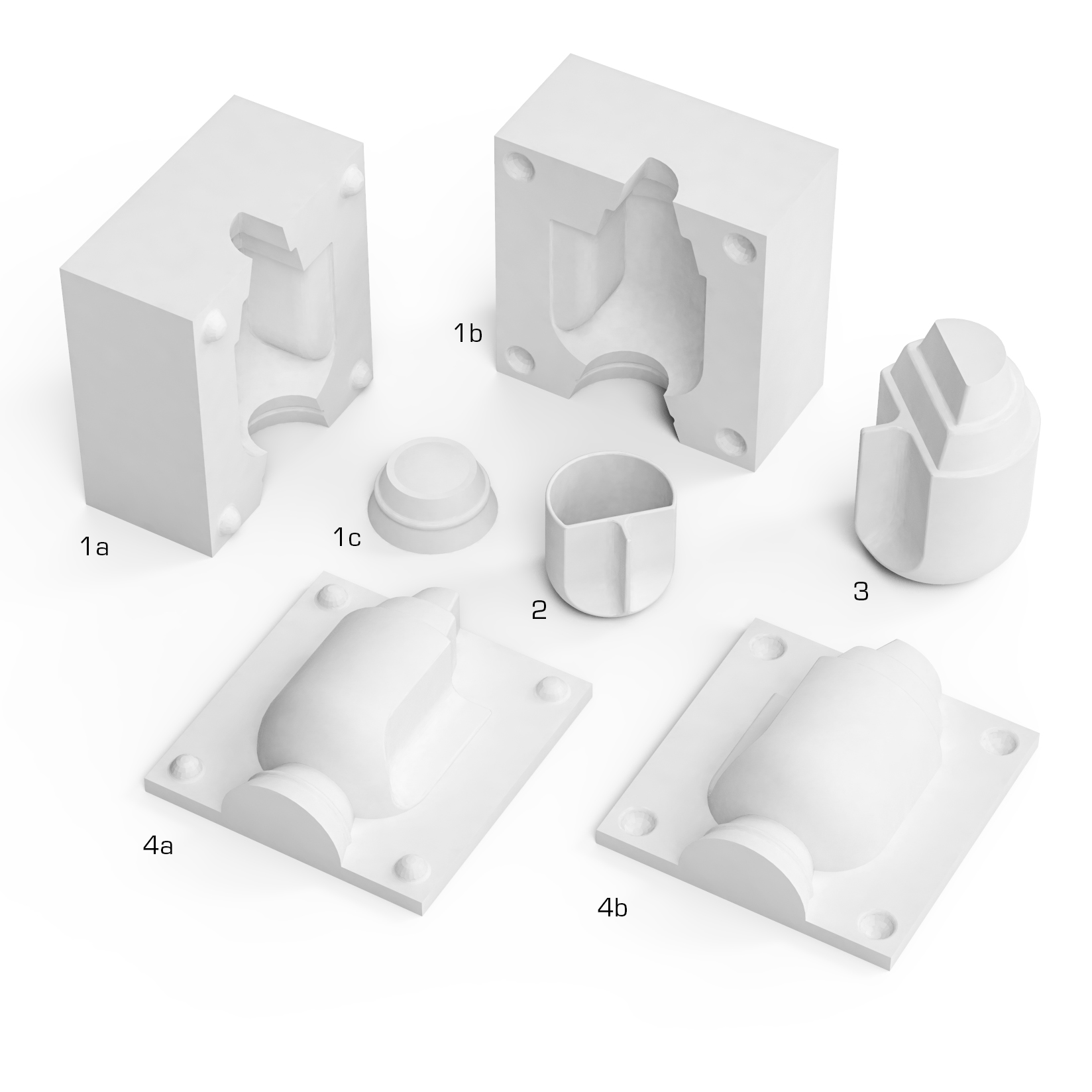
Here you can see an digital overview of the different elements of my research:
1 - Digital 3 part plaster mold design. This intended mold design after being cast off of the positive CNC or 3D print models.
1a -Mold left
1b -Mold right
1c -Bottom retainer
2 - Digital cup design. This is the intended result after being slipcast and fired.
3 - 3D printable positive for the casting of the plaster mold.
4 - CNC positive for the casting of the plaster mold.
4a - positive left
4b - positive right
Some elements to note:
-The plaster mold must be 10% larger than the final part because ceramics shrink when fired.
-On the top of the positives you will notice two stair steps. This is called a top spare and it allows for over filling of the plaster mold and increased strength of the part once it is removed from the mold. This is cut off prior to firing
-Half spheres on the plaster mold are for indexing to ensure the mold comes together in the right place every time.
In the following sections I will get into more detail on each process.
CNC Machining Mold Making
CNC machining is a very precise subtractive manufacturing technique. A endmill (similar to a drill bit) is spun at high speeds and computer controlled in 3+ axes to carve out a design from a block of material. This means CNC machining is highly suited to making larger models when compared to 3D printing because 3d printers must build up the extra volume. Because of this I chose to design each half of the final plaster mold as opposed to a single positive that would be cast in the traditional two steps.
To the right you can see the CNC program I made to create the positives for the plaster mold. Unfortunately due to the COVID-19 closures I was unable to finish manufacturing the mold.
Some notes on the missed opportunities:
-One of the issues I was running into with this process was successfully milling corners where walls intersect non-perpendicularly due to limitation in tooling I was going to recommend design guidelines to work around these weak points.
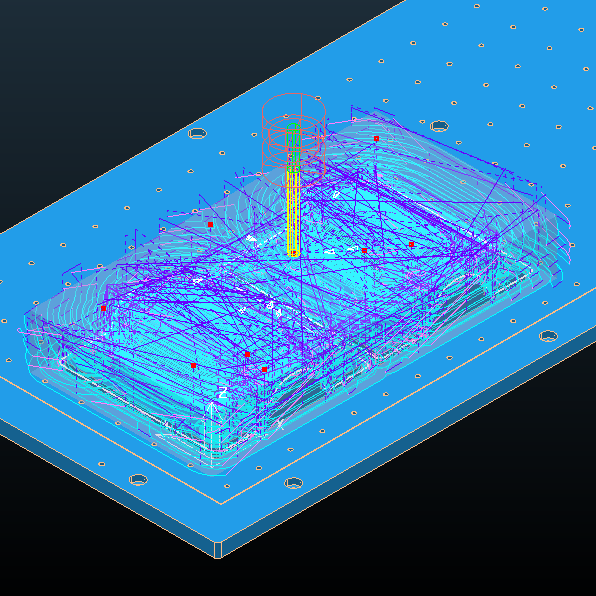
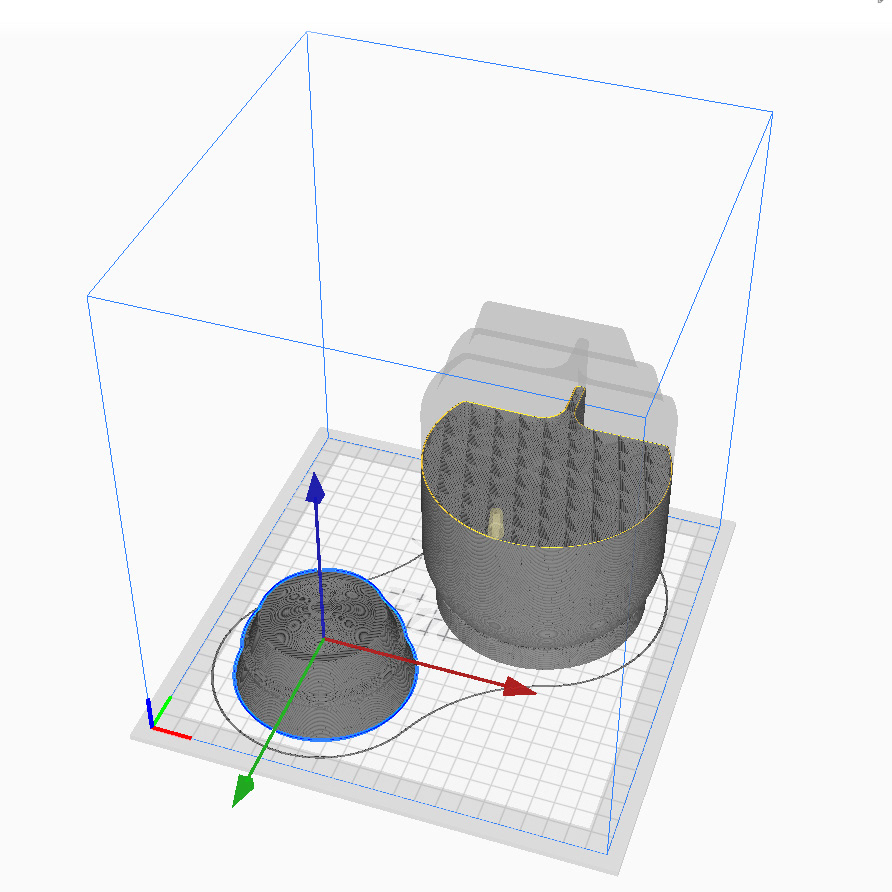
3d Printing Mold Making
The 3D printing strategy I settled on was similar to the traditional way of plaster mold making I described earlier only with the substitution of a 3D printed positive rather than a hand made one. The intended process is that a positive would be 3d printed then half of the positive would be cast in plaster and dried then the other half would be cast to ensure a two part mold. An additional bottom spare was added to allow for easier mold release once cast.
To the right you can see the positive and bottom spare being prepared for 3D printing on a computer. One of the major considerations when 3D printing is the orientation of the part. The mode of 3D printing I utilized is Fused Deposition Modeling (FDM). In this process plastic is extruded in space to create a desired form. This process however leaves stair stepping the height of each layer. If not controlled this can result in less-than-desirable surface finishes that would be transferred to the plaster mold and in turn the final ceramic part. After some experimentation I found that a vertical upright orientation worked the best.
I was able to work with my Mentor Colin Kilmesh to create a plaster mold off of a 3D print prior to the closure of the DAAP facilities. You can see the result below: both the 3D printed positive and the plaster negative.
Unfortunately I was not able to pursue this any further due to the shutdown. My intention was to see how this mold design preformed then make revisions.
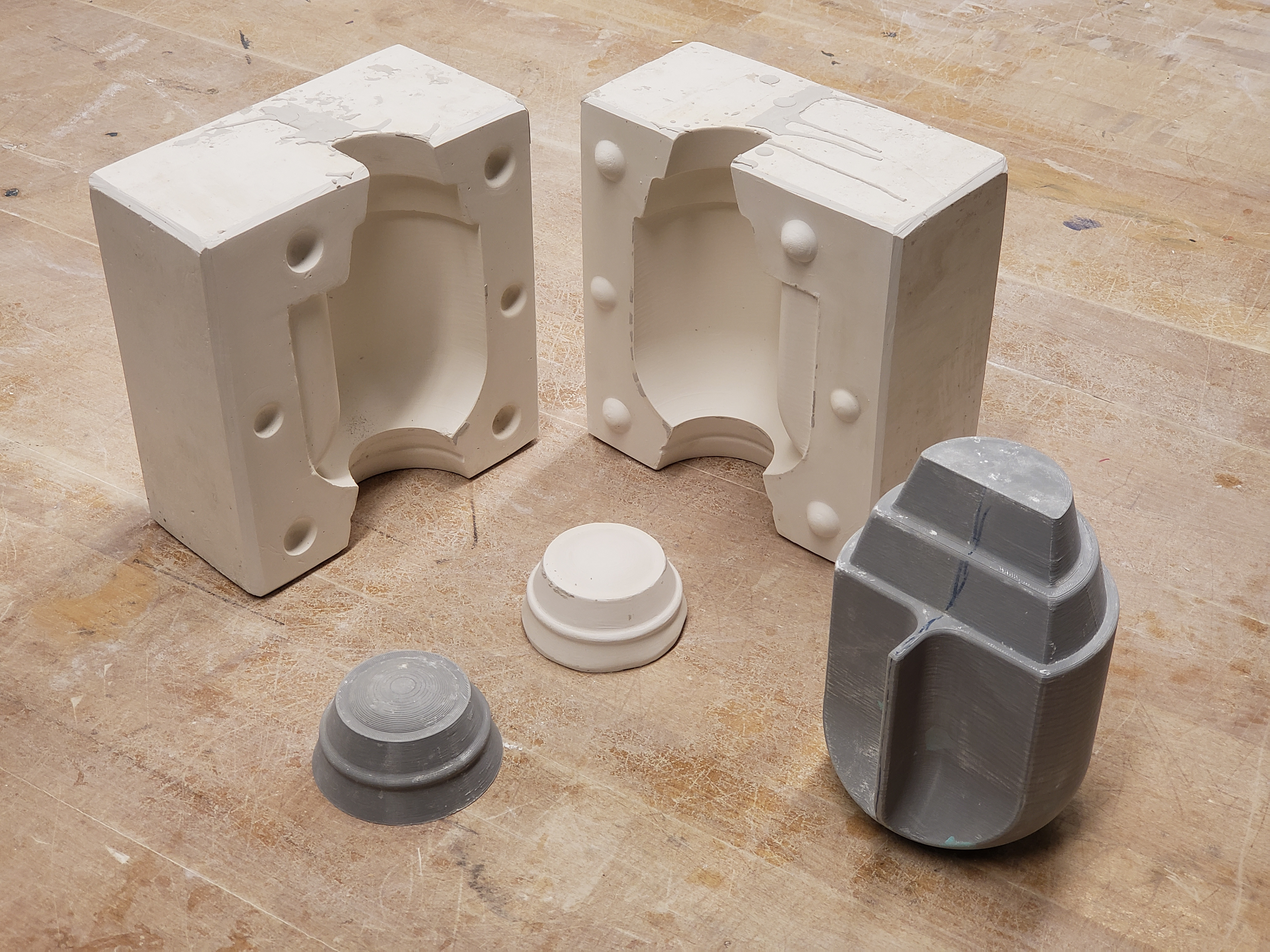